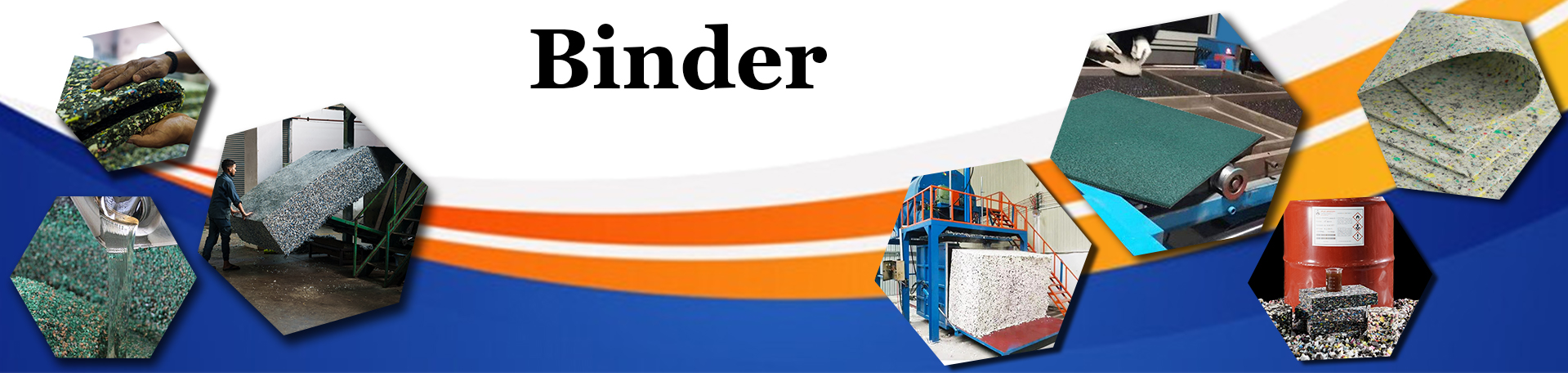
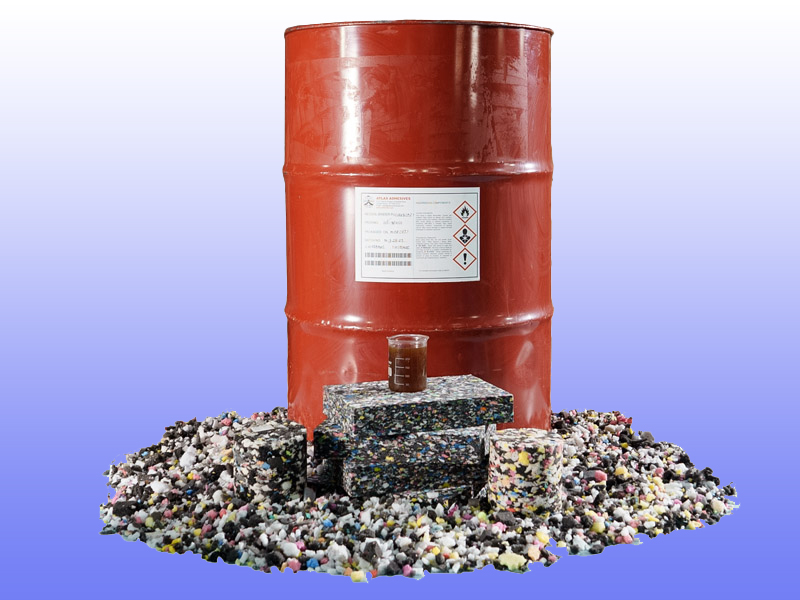
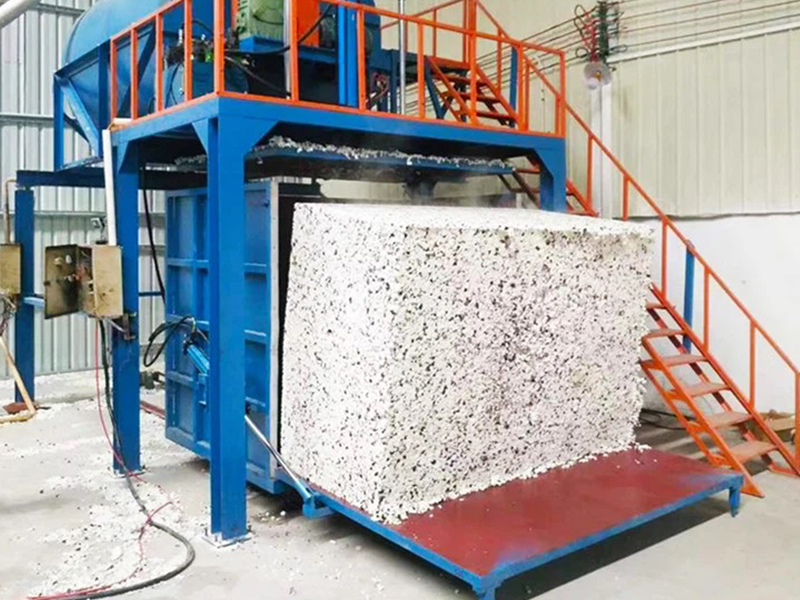
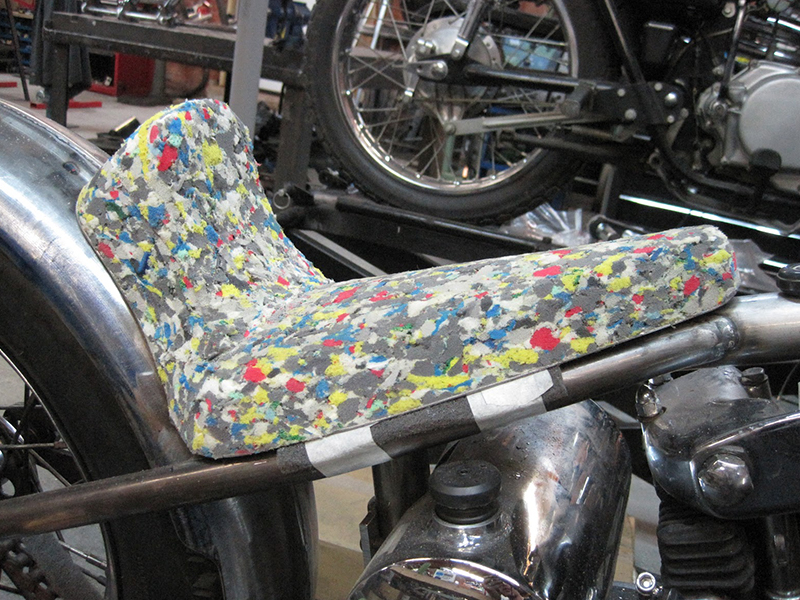
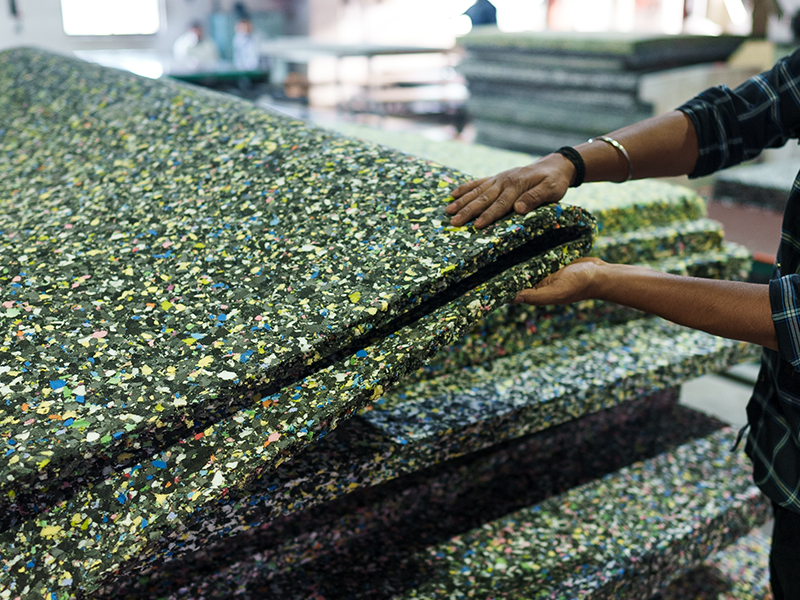
Foam Binder
A customized one-component polyurethane binder based on MDI, completely odorless and solvent, suitable for the production of various rebound foams. The customized one-component polyurethane binder based on MDI (Methylene Diphenyl Isocyanate) is a specialized adhesive formulation designed for the production of various rebound foams. Here's a detailed description of this binder and its key features:
Polyurethane Composition: The binder is primarily composed of polyurethane, a versatile polymer known for its excellent bonding properties and durability. Polyurethane binders are commonly used in foam production due to their ability to form strong bonds and provide flexibility.
MDI-Based Formulation: The binder is based on MDI, which is a type of isocyanate commonly used in polyurethane formulations. MDI offers excellent reactivity and contributes to the overall strength and resilience of the foam.
Compatibility with Rebound Foams: The binder is specifically formulated for use in the production of rebound foams, also known as rebound foams. These foams are typically made from recycled or reclaimed foam materials and require a binder to bond the shredded foam particles together to form new foam blocks or sheets.
Versatility: The binder is suitable for producing various types of rebound foams, including carpet underlay, athletic mats, cushioning pads, and soundproofing materials. Its versatility allows for the production of foam products with different densities, hardness levels, and compressive strengths.
Excellent Bonding Properties: The binder forms strong and durable bonds between foam particles, ensuring that the resulting rebound foam exhibits uniform density and resilience. This enhances the performance and longevity of foam products in various applications.
Customization Options: Manufacturers may have the flexibility to customize the formulation of the binder to meet specific requirements, such as adjusting the curing time, viscosity, or other properties to optimize production processes and foam performance.
Compliance with Regulations: The binder may comply with relevant industry standards and regulations governing foam production, ensuring that the resulting foam products meet quality and safety requirements for their intended applications.
Ease of Handling: The binder may be formulated for easy handling and application in foam manufacturing processes, whether through spray application, mixing with foam particles, or other methods. This facilitates efficient production and consistent foam quality.
Environmental Considerations: In addition to being odorless and solvent-free, the binder may be formulated to minimize environmental impact, such as by using sustainable raw materials or incorporating recycling initiatives into the foam production process.